Problem:
A steel
service center operates a mid-1970’s vintage 60" x .028"-.120" x 150 FPM
hump table-positive stop type cut-to-length line that was unable to hold
length and squareness tolerances that its customers were demanding. In
addition, the old sheet stacker was producing sloppy, staggered sheet packs
that were becoming unacceptable to its customers. Something had to be done
in order to maintain existing sheet and blank accounts; either purchase a
new CTL line for around $1 million, or if possible, upgrade the existing CTL.
Solution:
Coiltech
was commissioned to upgrade the existing CTL line to produce tight tolerance
sheets and blanks, increase productivity, and produce "solid block" finished
packages.
The
existing entry end equipment was saved, as was the leveler, shear, and
measuring table runout belt conveyor. The old hump table, positive stop, and
sheet stacker were discarded in favor of a new Precision Electronic Roll
Feed and a new Sheet Stacker and Weigh Station.
Development:
The new
equipment delivery schedule was established, and new CTL line engineering
drawings were prepared. About a week before the new equipment was due to
arrive, the old CTL line was de-commissioned to begin preparations for the
new line arrangement. The entry equipment through the leveler was left
untouched, remaining in existing locations, while the old hump table, shear,
measuring table, and stacker were removed. A shallow 20' long looping pit
was installed after the leveler, as was a new concrete footing for the old
shear. The new Servo Feed with the associated looping pit carryover tables
and loop quadrants was installed along with the old shear and measuring
table. Finally, the new Sheet Stacker with its elevating table and integral
scale was installed after the old measuring table was in place. The upgraded
CTL line was ready to run as a Precision Electronic Roll Feed Blanking Line.
Down time was about 2-1/2 weeks.
Results:
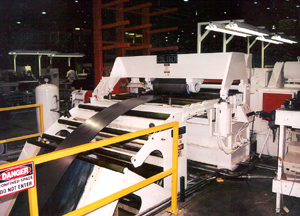
Precision Electronic Roll Feed
The
upgraded line was prepared to produce sheets and blanks to precision length
and diagonal tolerances, and was able to stack those sheets and blanks into
solid block packages. Productivity nearly doubled that of the old line
because; (1) the Servo Feed allows the leveler to run at a constant speed
rather than losing speed in its former slow down-positive stop cycle; (2)
new lengths are set-up by key pad operator input rather than trial and error
re-positioning a positive stop; (3) pack weights are recorded before removal
from the line, eliminating double handling; and (4) fresh pallets are power
injected into the stacker, minimizing time lost to unloading finished packs.
|
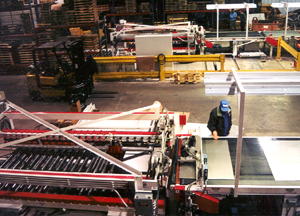
Automatic Sheet Stacker - Weigh Station
Allows Visual Sheet Inspection
Although the old measuring table belt conveyor
could have been eliminated from the new arrangement by installing the new
sheet stacker immediately behind the shear, the belt conveyor was
re-installed because it allowed each and every cut sheet to be visually
inspected for flatness and surface condition, and it allowed blanks to be
easily removed from the line for length and squareness verification without
interrupting production. Those operational benefits dictated the
re-installation of the runout belt conveyor.
Cost:
The cost to upgrade the existing CTL line to produce
close tolerance sheets and blanks was a small fraction of the cost of a new
CTL line. The increased productivity assured a quick return on the
investment, and the improved length and diagonal tolerances opened new
markets and assured the retention of existing accounts.
Conclusions:
Late 1960’s through early 1980’s hump table-positive stop
cut-to-length lines equipped with a corrective roller leveler are generally
well maintained and normally produce an acceptably flat sheet. But because
of the positive stop measuring system, they usually are deficient when it
comes to 21st century length and diagonal tolerance
demands and productivity. It is cost effective to upgrade those CTL lines by
replacing the hump table-positive stop measurement system with a
"state-of-the-art" electronic roll feed system. The new microprocessor based
motion control electronics are operator friendly, extremely reliable, and
incredibly accurate. As compared to "mechanical" type feed devices, the
electronic roll feed occupies much less space and offers quicker set-up
time, lower operating costs, significantly lower maintenance costs, and has
a significantly longer operational life expectancy.
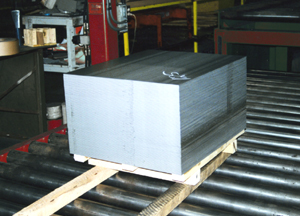
Solid Block Steel Packs |